Jak często wzorcować czujnik?
Kalibracja jest ważna wyłącznie w momencie jej przeprowadzenia. Jednak w praktyce często pojawiającym się pytaniem jest: jak często należy przeprowadzać ponowną kalibrację? Generalnie operator układu pomiarowego jest odpowiedzialny za określenie interwałów kalibracji. Jeżeli w zakładzie dostępna jest wewnętrzna specyfikacja ponownych kalibracji np. w instrukcji zarządzania jakością, to staje się ona oficjalnym źródłem dla harmonogramu rekalibracji. Dla niektórych zastosowań stosuje się wprost wytyczne ogólnych norm (np. ISO376 dla przyrządów do pomiaru siły).
Kalibracja musi być przeprowadzona zarówno przed, jak i po każdym istotnym pomiarze. Przykładami takich aplikacji są pomiary w ramach akredytacji oprzyrządowania kalibracyjnego DKD lub pomiary w ramach certyfikacji silnika pojazdu zgodnie z przepisami dotyczącymi emisji spalin.
Przy bardziej pragmatycznym podejściu w praktyce przemysłowej, jakie zaleca norma ISO10012, jest bardziej sensowne, aby umożliwić większą liczbę pomiarów lub określony okres pomiędzy dwiema kalibracjami. Jeżeli odchyłki zmierzone podczas kalibracji w porównaniu z wartościami z poprzedniej kalibracji mieszczą się w zakresie wymagań metrologicznych, wtedy wyniki pomiaru uzyskane za pomocą oprzyrządowania pomiarowego są uzasadnione. Jeżeli jednak odchyłki są większe, wtedy pojawia się pytanie, czy pomiary są znaczące jedynie w ograniczonym zakresie i czy powinny zostać powtórzone. Decyzja odnośnie do tego, jak długi powinien być okres między kalibracjami, musi wtedy brać pod uwagę, jak wysokie są z jednej strony koszty częstszych kalibracji (łącznie z utratą czasu potrzebnego na kalibrację), a z drugiej strony bezużytecznych wyników pomiarów, powtarzania pomiarów, czynności itp.
Ważnym aspektem jest również prawdopodobieństwo zaistnienia zmian we własnościach pomiarowych, które mogą skutkować znaczącymi odchyłkami wyników pomiędzy jedną a drugą kalibracją. Z punktu widzenia jakości łatwo jest ustalić, że określone warunki mogą wymagać częstszych kalibracji, np. takie jak wysokie liczby godzin pracy (praca zmianowa), ekstremalne warunki termiczne, praca przetworników przy zmiennym obciążeniu w długim czasie, brud i wilgoć. Jednak aby określić wymierne stanowisko odnośnie do używanego oprzyrządowania pomiarowego przy pomocy danych producenta, wymagane są szerokie dane statystyczne dla każdego typu przetwornika lub elektroniki pomiarowej, które są zwykle niedostępne. Operator układu pomiarowego może jednak uzyskać dobre rezultaty poprzez ciągłe śledzenie wyników kalibracji i długoterminowego zachowania się używanego oprzyrządowania w warunkach pracy istotnych dla aplikacji.
Innymi słowy: jeżeli sprzęt pomiarowy jest używany w stanowisku testowym, w którym warunki pracy są trudne, koszty wysokie, a wyniki pomiarów są reprezentowane na późniejszym etapie i okazują się niewiarygodne, to może okazać się sensowne, by przeprowadzać ponowną kalibrację po 6 lub nawet po 3 miesiącach. Jeżeli jednak po pierwszej lub drugiej kalibracji staje się jasne, że własności pomiarowe pozostają stabilne w dłuższym czasie, to można zadecydować tym samym o wydłużeniu okresu pomiędzy kalibracjami. Taka procedura określania, pod jakimi warunkami okres między kalibracjami może być wydłużony, powinna być częścią systemu zarządzania jakością. I powinna również określać skracanie okresów międzykalibracyjnych np. w wyniku zużycia lub zjawiska dryftu.
Pomiary porównawcze kilku skalibrowanych przyrządów testowych są kolejnym argumentem przy podejmowaniu decyzji odnośnie do adaptacji interwałów kalibracji. Gdy np. laboratorium testujące używa kilku przetworników siły i posiada oprzyrządowanie potrzebne do pomiarów porównawczych – to takie porównania mogą wykazać, czy interwał kalibracji, który początkowo był skalkulowany, powinien być skrócony.
Znaczenie warunków pracy oznacza, że ponowne wzorcowanie należy przeprowadzić w każdym przypadku, gdy narzędzie pomiarowe jest poddane np.: naprężeniom, które leżą poza zamierzonym zakresem, większym przeciążeniom, upadkom, ekstremalnym temperaturom lub naprawom.
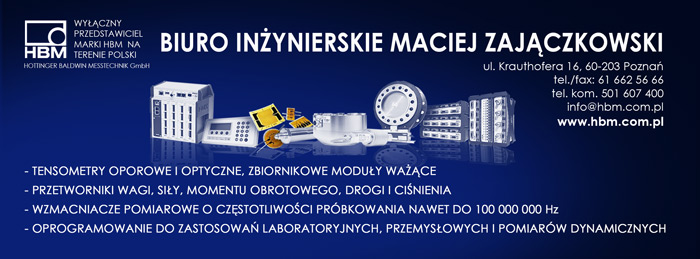