Nowoczesny silnik do napędu wysoko wydajnego wentylatora o zmiennej geometrii
Jacek Przybyłka
W wyniku ciągłego rozwoju produktów przeznaczonych do napędu specjalistycznych maszyn i urządzeń firma DFME DAMEL SA opracowała rodzinę silników przeznaczonych do napędu wentylatorów o dużej i zmiennej wydajności. Jednym z tego typu silników jest silnik typu S1 710Y-8 o mocy 1800 kW. Widok silnika przedstawiono na rys. 1.
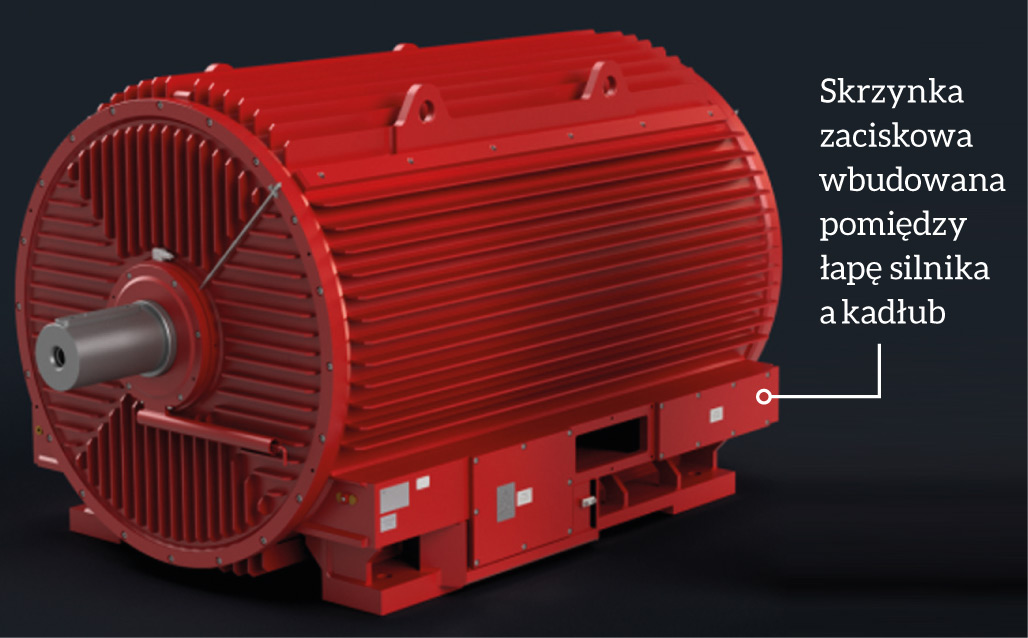
Rys. 1. Silnik S1 710Y-8
Prace konstrukcyjne zostały przeprowadzone we własnym biurze konstrukcyjnym DFME DAMEL SA przy wykorzystaniu komputerowego programu wspomagania projektowania i modelowania 3D, analizy termodynamicznej oraz analizy wytrzymałościowej metodą elementów skończonych (MES).
Silnik został zaprojektowany pod kątem zabudowy w lutni do napędu wentylatora o dużej średnicy i zmiennej wydajności. Zmiana wydajności realizowana może być poprzez zmianę geometrii łopat lub regulację prędkości poprzez zasilanie z przemiennika częstotliwości. Konstrukcja silnika została zoptymalizowana pod kątem minimalizacji oporów aerodynamicznych strugi powietrza opływającej silnik, odporności uzwojenia na duże stromości narastania napięci, du/dt oraz wpływu na pracę silnika harmonicznych, występujących przy zasilaniu z przemiennika częstotliwości. Zaprojektowano również specjalnej konstrukcji wirnik o obniżonym momencie bezwładności i jednocześnie największym możliwym momencie obrotowym oraz węzły łożyskowe o wydłużonej trwałości i odporne na prądy łożyskowe.
Miejsce zabudowy silnika wewnątrz lutni i napęd wentylatora lutniowego były głównym kryterium przy projekcie kadłuba, który został zaprojektowany tak, aby stanowił jak najmniejszy opór aerodynamiczny dla opływającej go strugi powietrza. Optymalizacja oporów aerodynamicznych ma istotny wpływ na całkowitą sprawność wentylatora oraz skuteczność chłodzenia silnika. W tym celu zastosowano specjalną konstrukcję skrzynki zaciskowej wbudowanej w przestrzeń pomiędzy łapą a kadłubem silnika (rys. 1).
Aby ułatwić podłączenie silnika w różnych aplikacjach, zastosowano symetryczny układ dwóch identycznych skrzynek zaciskowych umiejscowionych po obu stronach silnika. Dodatkowo zwarta konstrukcja zapewnia dużą sztywność kadłuba, dzięki czemu poziom drgań wywoływanych przez silnik został ograniczony do minimum.
Ze względu na docelowe zastosowanie silnika do napędu wentylatorów o dużej średnicy istotnym parametrem było maksymalne obniżenie masy i momentu bezwładności wirnika. Uzyskano to dzięki zoptymalizowanej szkieletowej konstrukcji wirnika oraz zastosowaniu jednoklatkowego układu obwodu elektromagnetycznego. Taka konstrukcja pozwoliła na redukcję masy wirnika o 30% oraz zmniejszenie jego momentu bezwładności o 20%. Szkieletowa konstrukcja i powstałe wewnętrzne kanały wentylacyjne oraz zastosowany rewersyjny system przewietrzania wirnika pozwoliły na obniżenie i ustabilizowanie się temperatury wału i obwodu elektromagnetycznego bez względu na kierunek wirowania. Tak zaprojektowany układ przewietrzania, wykorzystujący wewnętrzne kanały wentylacyjne działające jak zintegrowany wymiennik ciepła, pozwolił również na chłodzenie osprzętu wewnątrz skrzynek zaciskowych.
Układ łożyskowania zaprojektowano z zastosowaniem podwójnego układu łożysk po stronie napędowej, gdzie zastosowano łożysko kulkowe i łożysko walcowe. Pozwala to na maksymalne zwiększenie nośności i umożliwia współpracę z wentylatorem o dużej średnicy. Po stronie przeciwnapędowej zastosowano łożysko walcowe izolowane, co stanowi skuteczne zabezpieczenie układu łożyskowania przed degradacją powodowaną przez prądy łożyskowe występujące przy zasilaniu silnika z przemiennika częstotliwości. Dodatkowo w celu wydłużenia trwałości układu łożyskowania zastosowano układ współpracujący z automatycznym systemem podawania smaru do łożysk. Po obu stronach zastosowano żebrowane tarcze łożyskowe i odpowiednie uszczelnienia wału zapewniające stopień ochrony IP66.
Uzwojenie stojana zaprojektowano z profilowego przewodu miedzianego z zastosowaniem porowatych materiałów izolacyjnych w klasie izolacji H, przeznaczonych do impregnacji próżniowo-ciśnieniowej VPI. Dodatkowo zastosowano zabezpieczenie cewek przed zjawiskami jarzeniowymi poprzez zastosowanie taśmy przewodzącej i półprzewodzącej. Zastosowanie najnowocześniejszych materiałów izolacyjnych pozwoliło w maksymalnym stopniu wykorzystać możliwości konstrukcyjne i technologiczne stosowane w procesie produkcji uzwojeń silników na napięcia znamionowe 6 kV.
Uzwojenie stojana impregnowane jest metodą próżniowo-ciśnieniową w żywicach epoksydowych o ograniczonej emisji do atmosfery substancji szkodliwych, a następnie suszone w suszarkach z kontrolą temperatury i rejestracją przebiegu procesu. Wysuszona i utwardzona żywica wypełniająca całkowicie układ izolacyjny uzwojenia stojana stanowi z nim monolit odporny na większość agresywnych oddziaływań środowiska pracy, znacznie poprawia przewodzenie ciepła i schładzanie uzwojenia. Rezystancja izolacji uzwojeń sięga do kilkudziesięciu GΩ. Widok cewki i kompletnego stojana przedstawiono na rys. 2.
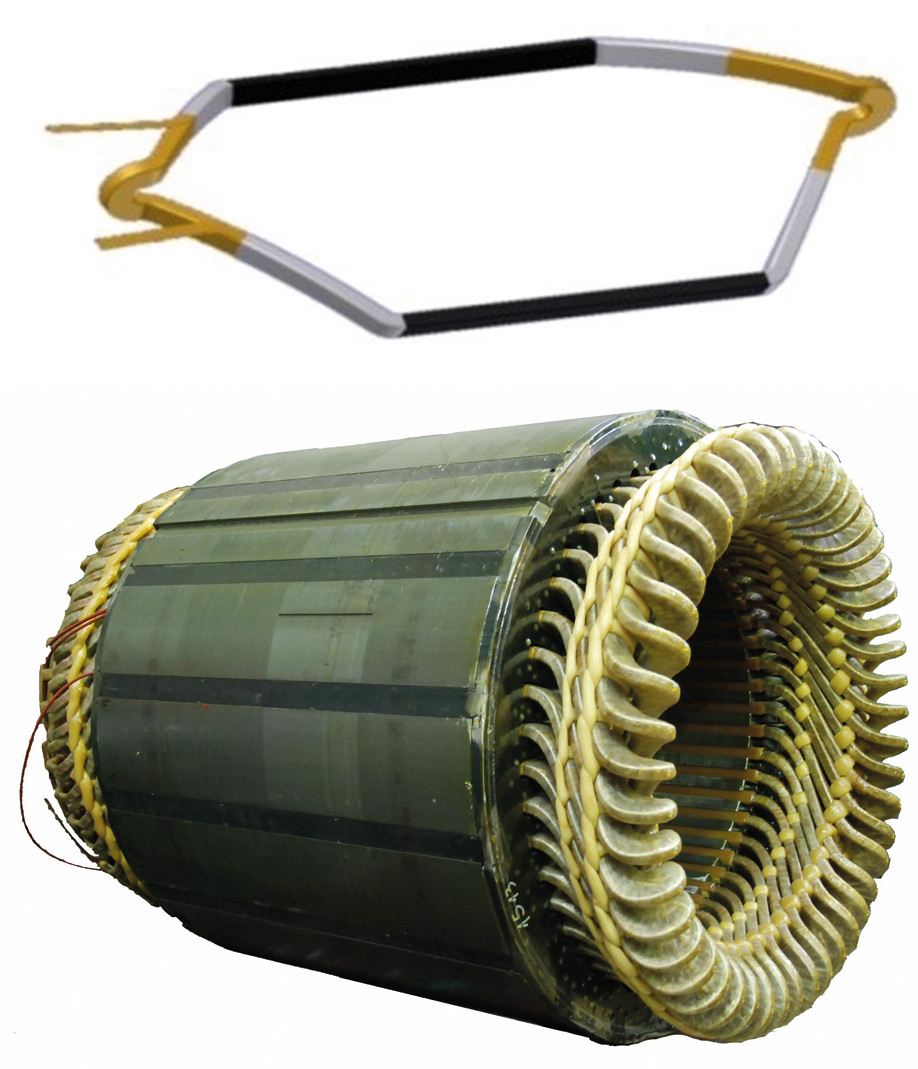
Rys. 2. Cewka i rdzeń stojana uzwojony silnika 6000 V
W wyniku wielowariantowych obliczeń ostatecznie uzyskano optymalne parametry silnika. Ich podstawowe wartości przedstawiono w tabeli 1. Zastosowanie komputerowych technik obliczeniowych pozwoliło uzyskać zmniejszenie masy silnika, obniżenie momentu bezwładności oraz maksymalne obniżenie oporów aerodynamicznych zabudowanego silnika w lutni.
Tabela 1. Optymalne parametry silnika
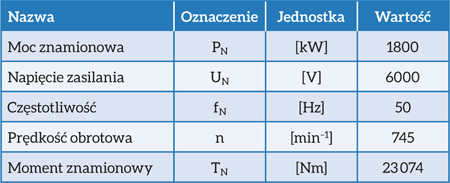
W związku z postawionymi wymaganiami, dotyczącymi sposobu zasilania silnika (przemiennik częstotliwości), w realizacji projektu zastosowano konstrukcję z wirnikiem jednoklatkowym, która jest optymalnym rozwiązaniem dla tego typu zastosowań. Takie rozwiązanie daje do dyspozycji wysoki moment krytyczny wykorzystywany przy zasilaniu z przemiennika częstotliwości przy jednoczesnym obniżeniu masy wirnika ze względu na obecność tylko jednej klatki. Przykładowy przebieg charakterystyk momentu w funkcji obrotów pokazano na rys. 3.
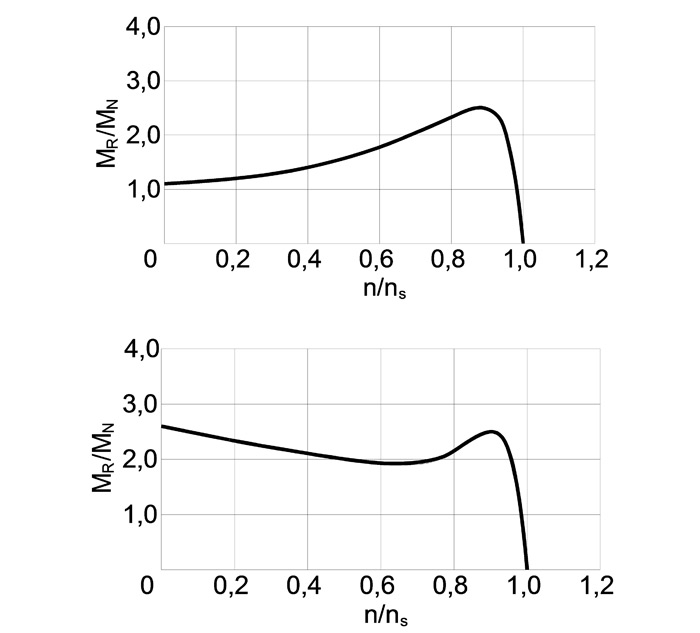
Rys. 3. Przykładowy przebieg charakterystyk momentu w funkcji obrotów (częstotliwości zasilania) dla wirnika jednoklatkowego (u góry) i dwuklatkowego (u dołu)
Zastosowanie wirnika jednoklatkowego i zasilanie silnika z przemiennika częstotliwości pozwala w każdym punkcie charakterystyki silnika T = f(n) pracować w pobliżu momentu krytycznego, co poglądowo przedstawiono na rysunku 4.
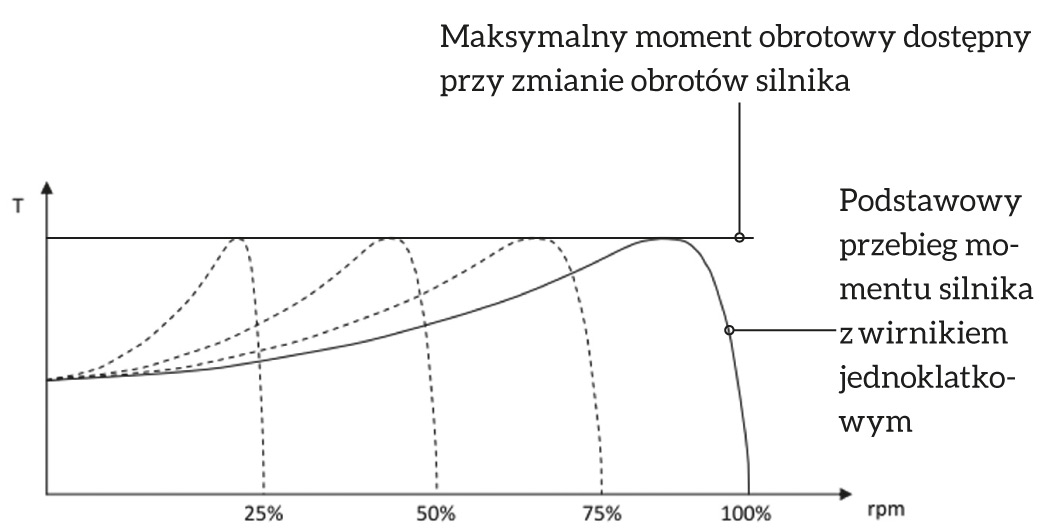
Rys. 4. Przebieg momentu w funkcji obrotów silnika indukcyjnego z wirnikiem jednoklatkowym zasilanym z przemiennika częstotliwości
W docelowej konfiguracji silnik posiada szereg zabezpieczeń oraz elementów pozwalających na diagnostykę i sterowanie pracą silnika. Wewnątrz silnik posiada zamontowany układ ochrony termicznej oraz elementy zabezpieczające przed gromadzeniem się wilgoci w postaci kondensatu.
Dla zabezpieczenia przed przekroczeniem dopuszczalnej temperatury silnika zastosowano niezależne obwody czujników w uzwojeniu i tarczach łożyskowych, których obwody zostały wyprowadzone do skrzynki zaciskowej i przystosowane do włączenia w zewnętrzny obwód sterowania. Do zabezpieczenia uzwojenia zastosowano dwa obwody czujników temperatury, złożone z elementów dwustanowych PTC lub bimetali oraz czujników PT100 umożliwiających ciągły pomiar temperatury. Elementy PT100 zostały zastosowane także w tarczach łożyskowych i wraz z elementami pomiarowymi z uzwojenia tworzą pełny monitoring temperatury silnika, pozwalający na wczesne wykrycie jego stanów awaryjnych.
Dla ograniczenia zjawiska kondensacji pary wodnej wewnątrz silnika, mogącej powodować zawilgocenia uzwojenia i w konsekwencji obniżenie wartości rezystancji izolacji, silnik jest wyposażony w dwie grzałki antykondensacyjne zabudowane wewnątrz kadłuba. Grzałki te mogą być włączone tylko w czasie postoju silnika i muszą być wyłączane przed jego załączeniem.
Silnik w docelowej zabudowie jest wyposażony dodatkowo w hamulec, enkoder oraz czujniki drgań. Zabudowę silnika w obudowie wentylatora (lutni) pokazano na rys. 5.
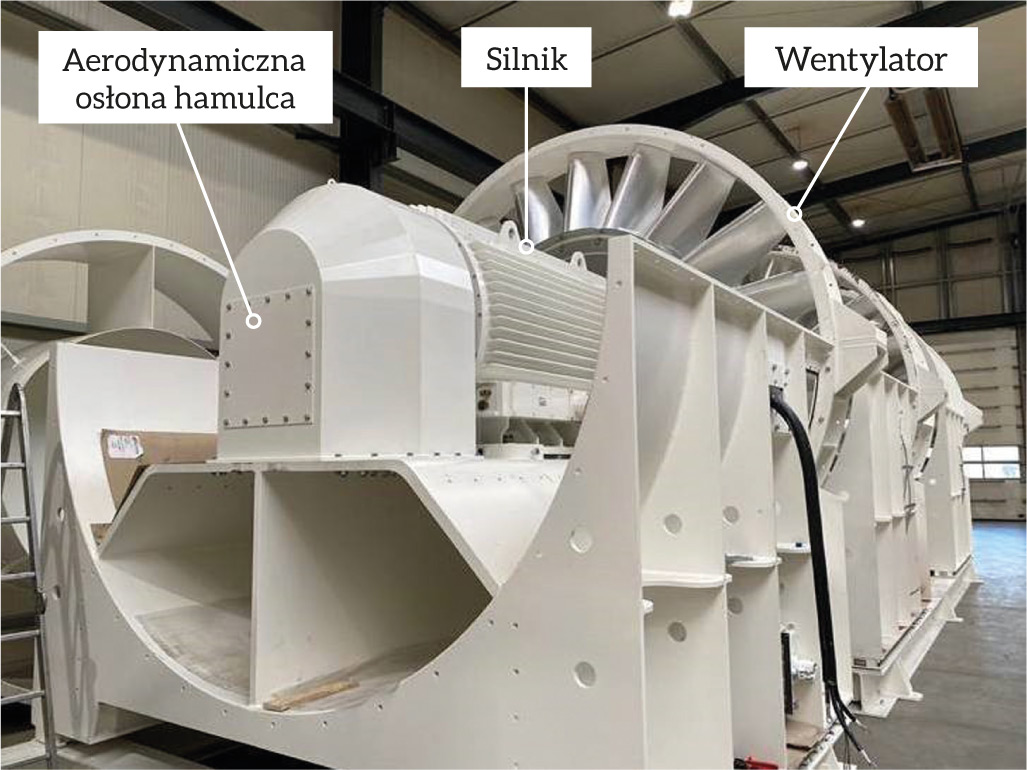
Rys. 5. Silnik w trakcie zabudowy w lutni
W celu umożliwienia montażu hamulca postojowego i enkodera silnik wyposażono w specjalnie przedłużony wał po przeciwnej stronie wentylatora. Na jego końcu pod aerodynamiczną osłoną montowany jest hamulec oraz enkoder służący do pomiarów prędkości obrotowej silnika. Sygnał z enkodera wykorzystywany jest do sterowania przemiennika częstotliwości i optymalizacji wydajności całego zestawu wentylacyjnego a także, w momencie zatrzymania silnika, do uruchomienia hamulca postojowego. Dodatkowo silnik jest przystosowany do zamontowania czujników drgań montowanych do pokryw łożyskowych zewnętrznych po stronie napędowej i przeciwnapędowej.
Wszystkie sygnały z czujników zastosowanych do zabezpieczenia, sterowania i monitoringu stanu pracy silnika wyprowadzone są do skrzynek zaciskowych umieszczonych po obu stronach silnika z możliwością podłączenia z lewej, jak i z prawej strony lutni.
Opracowana konstrukcja silnika S1 710Y-8, opisana w niniejszym artykule, potwierdza, że w celu osiągnięcia wysokich parametrów projektowanego napędu niezbędna jest analiza każdego najdrobniejszego szczegółu mającego wpływ na osiągnięte parametry.
Nie bez znaczenia jest posiadanie wiedzy wynikającej z wieloletniej działalności projektowej w dziedzinie napędów elektrycznych, jaką posiadają konstruktorzy w DFME DAMEL SA.
Zdobyte doświadczenie w opracowaniu konstrukcji silników pracujących w wielu różnorodnych napędach pozwala szybko i skutecznie realizować najbardziej zaawansowane konstrukcje i osiągać założone parametry napędu.
Autor:
Jacek Przybyłka – Dział Rozwoju
Dąbrowska Fabryka Maszyn Elektrycznych „DAMEL” SA
41-300 Dąbrowa Górnicza, Al. J. Piłsudskiego 2
e-mail: jprzybylka@damel.com.pl
Dąbrowska Fabryka Maszyn Elektrycznych „DAMEL” SA
Aleja Józefa Piłsudskiego 2
41-300 Dąbrowa Górnicza
tel. 32 262 32 31
fax 32 264 34 26
fax dział sprzedaży: 32 264 10 12
e-mail: office@damel.pl
www.damel.pl
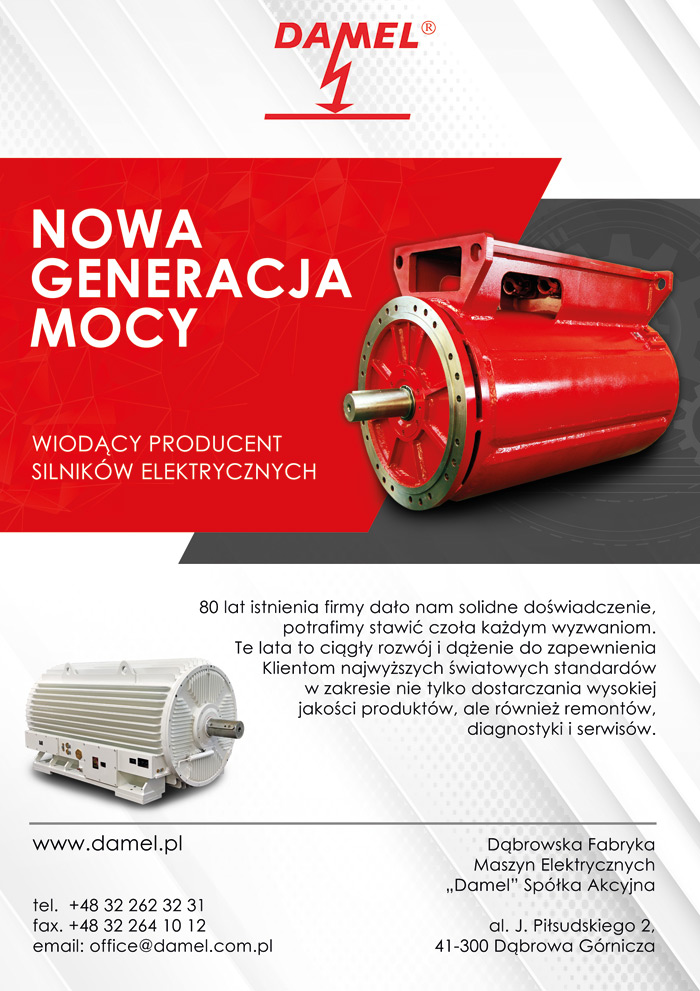