Po co nam ten cały Przemysł 4.0?
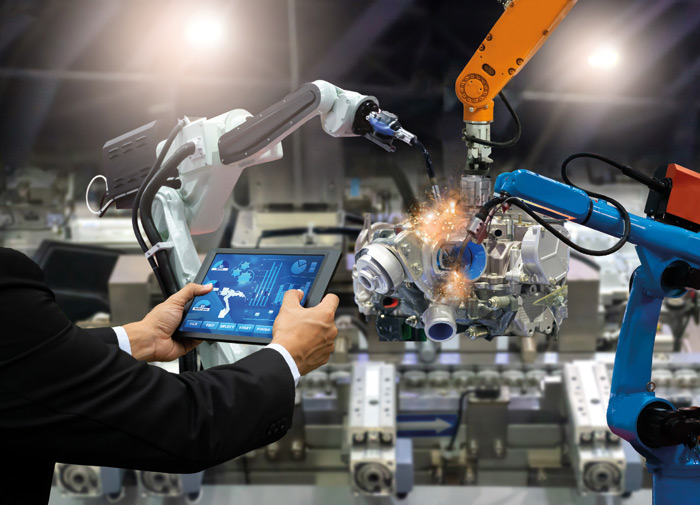
O możliwościach wdrożenia Przemysłu 4.0 i potencjale cyfryzacji polskich przedsiębiorstw mówi Product Manager Grupy 4.0 w firmie Multiprojekt.
Redakcja: – Po co jest Przemysł 4.0? Czy to rzeczywiście odpowiedź na wszystkie problemy przedsiębiorstw, czy po prostu najszybszy skrót do wykorzystania nowych technologii?
Multiprojekt: – Dobre pytanie. Odpowiem przykładem wyjętym z życia. Po co nam są smartfony, skoro zwykłe telefony nam wystarczały? Nieubłaganie wpisujemy się w trend cyfryzacji wszystkiego, jesteśmy w to wpisani, więc to samo dotknęło przemysłu. Naturalną ścieżką rozwoju jest droga cyfryzacji przemysłu. A wbrew pozorom nie jest to branża, która obfituje w nowinki technologiczne. Oczywiście, jeżeli mówimy o automotive, to tych nowości jest sporo. Sama kultura pracy, środowisko, w jakim tworzone są samochody, pociągają za sobą konieczność automatyzacji. Większość firm nie posiada jednak wysokiego stopnia automatyzacji. Nasze zasoby polskie dalej się opierają na ludziach. Oni są niezbędni w niektórych procesach produkcyjnych, natomiast dozór bieżący ich pracy czy dozór produkcji następuje organoleptycznie. Jest osoba, która sprawdza, weryfikuje, potem wprowadza dane do systemu. Następnie ktoś te dane w systemie analizuje. Uważam, że cyfryzacja w przemyśle idzie w tym kierunku, żeby te dane pozyskiwać automatycznie z procesu produkcji, z różnych obszarów firmy i za pomocą algorytmów, sztucznej inteligencji lub zwykłych analiz przetwarzać je w trybie online tak, żeby można było reagować na bieżąco na to, co się dzieje na produkcji w firmie.
R.: – A to nie jest trochę tak, że te wszystkie dane statystyczne, które pokazują, że stopień automatyzacji w Polsce jest dużo niższy niż w Europie Zachodniej, wynikają z modelu gospodarczego, gdzie dominują małe i średnie firmy, które nie produkują aż tyle, żeby istniała potrzeba automatyzacji?
M.: – Porównywanie polskiego przemysłu z przemysłem Europy Zachodniej jest trochę analogiczne do porównywania produktywności polskiego pracownika do odpowiednika na Zachodzie. Statystyki pokazują, że jako Polacy pracujemy dużo, natomiast niekoniecznie bardzo produktywnie w stosunku do naszych zachodnich sąsiadów. Tak samo jest z przemysłem. Produkujemy dużo, dobrej jakości rzeczy, co nie zmienia faktu, że produkujemy je w sposób prosty nie tyle pod względem technologicznym, co jeśli chodzi o zarządzanie produkcją. Główną niepewnością, która dręczy przedsiębiorców, jest to, czy jeżeli zainwestują w tak zwaną technologię „Przemysł 4.0”, jakąkolwiek modernizację w zakresie przepływu informacji, czy to w ogóle się będzie kalkulowało. Dalej niestety tkwimy w tym sposobie myślenia, że najlepszą alternatywą jest dokupienie następnej maszyny i zatrudnienie kolejnych pięciu czy dziesięciu osób. Ten trend jest mało przyszłościowy, ponieważ niezależnie od tego, jak będziemy zaklinać rzeczywistość, nie sprawimy, że ona się zmieni w najbliższym czasie. Mam na myśli to, że nieubłaganie maszyny wyprą pracowników. Bez znaczenia jest to, jak duży będziemy mieli dostęp do siły roboczej. Ostatnie dwa lata pokazują jednak, że dostęp jest ograniczony. Zasoby ludzkie kurczą się, widzimy tzw. rynek pracownika, większość firm ma kłopoty z zatrudnianiem pracowników do produkcji, więc naturalnie będziemy musieli iść w stronę cyfryzacji i robotyzacji. Wracając do sedna pytania, obawa przed nieznanym. Większość polskich firm, małych, rodzinnych czy też z niewielkim kapitałem, które się dopiero rozwijają, boi się tych nowinek technologicznych, boi się wdrożenia, ponieważ nie zna się na tym. To wynika z czysto ludzkich reakcji, boimy się czegoś, czego nie znamy. Zwykle jeżeli czegoś nie znamy, boimy się, staramy się iść znanymi ścieżkami. W tym przypadku tą znaną ścieżką w polskim przemyśle jest mimo wszystko inwestowanie w maszyny, doposażanie parku maszynowego i zwiększanie ilości pracowników. Nie idziemy jeszcze w stronę technologiczną, to są dopiero nasze początki. Te obawy, niepewność ustawodawcza na ten moment oraz brak finansowań zewnętrznych powodują zastój i barierę w drodze do automatyzacji.
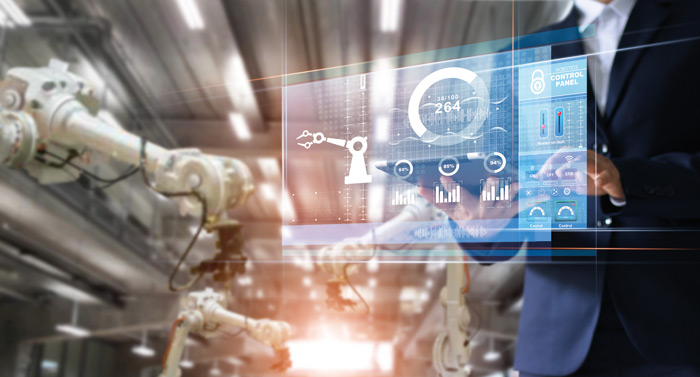
R.: – Z punktu widzenia przedsiębiorcy czy takie wdrożenie ma sens? Co mi to wdrożenie da, czy wyjdę na tym rzeczywiście na plus? Nawet jeśli mam małą firmę?
M.: – Sens na pewno ma. Czy jest ekonomicznie uzasadnione, to jest inna kwestia. To wynika ze specyfiki każdej firmy, natomiast nie ma sensu zaklinać rzeczywistości, że będzie inaczej niż to, co już powiedzieliśmy, czyli że ludzi na rynku pracy przybędzie, dlatego trzeba będzie i tak pójść w automatyzację. Pokrewnym tematem, który mogę podać jako przykład, są obecne problemy z energią elektryczną i z surowcami naturalnymi. One się wyczerpują, szukamy jakichś alternatyw i to, co do tej pory funkcjonowało przez ostatnich kilkanaście lat, że ceny prądu i gazu były na stałym poziomie i determinowały koszty produkcji, uległo w jednym momencie zmianie. Nie da się w sposób przewidywalny zaplanować kosztów. Jeżeli chodzi o wdrożenie Przemysłu 4.0 czy jego elementów, to nie musimy całego Przemysłu 4.0 wdrażać od razu, możemy zacząć od jakiejś jego części składowej, uruchomić część adekwatną dla potrzeb firmy. Przed wdrożeniem naturalnie należy zrobić analizę, czy nam się to opłaca. Jeżeli stwierdzimy, że tak, musimy brać pod uwagę takie czynniki, jak oszacowanie, co może podrożeć, jakie będą problemy z zasobami ludzkimi, jak technologia pójdzie do przodu i – co najważniejsze – czy utrzymamy się na rynku. Zachodnie firmy mają ekspansję w zakresie wdrażania Przemysłu 4.0 i prawda jest taka, że ich przewaga rośnie z dnia na dzień przy wdrażaniu tych technologii. Roboty i systemy nie generują przestojów, nie chorują tak jak pracownicy, a dobrze skrojony system gwarantuje sprawnie działające przedsiębiorstwo. Jeżeli popatrzeć na model polski, to przedsiębiorstwa zazwyczaj są zarządzane jednotorowo, ukierunkowane są na zysk, nie na rozwój technologii, który wspomaga generowanie zysku.
R.: – Jeżeli jestem zainteresowany wdrażaniem rozwiązań Przemysłu 4.0 w mojej firmie, ale nie mam możliwości przeprowadzenia analiz opłacalności, gdzie mam szukać rozwiązania, kogoś, kto byłby w stanie mi powiedzieć, czy to mi się opłaca czy nie?
M.: – Tematy technologiczne nie są przyswajalne tak od razu. Też musieliśmy się całkiem niedawno oswajać z nowymi technologiami. Nawet pandemia wymusiła nowe wzorce zachowań, jeżeli chodzi o zakupy czy obsługę urządzeń elektronicznych. Tak samo jest z Przemysłem 4.0. Musimy poszukać firmy, która ma wiedzę, ma zasoby i tzw. know how, jak zrobić tego typu wdrożenie. W ramach koniecznego audytu taka firma jest w stanie oszacować, czy ten zakład czy daną linię produkcyjną można restrukturyzować, cyfryzować. Istotne jest to, żeby taka firma miała doświadczenie praktyczne przy takich wdrożeniach, nie wyłącznie teoretyczne.
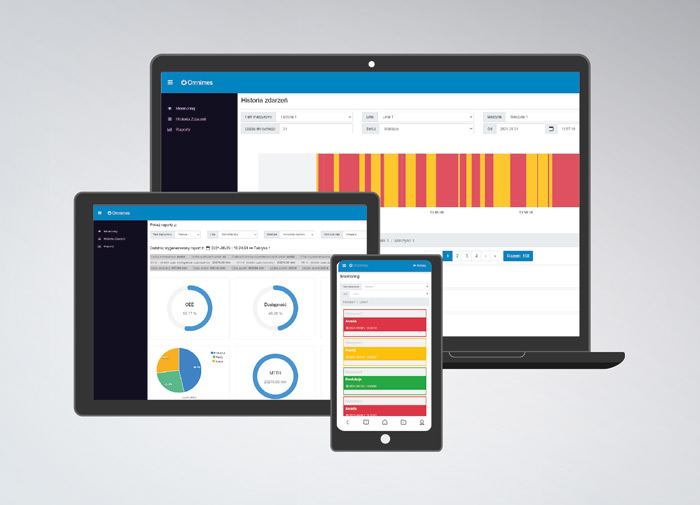
R.: – Z jednej strony mamy kwestię postawienia robota, stanowiska zautomatyzowanego. A co z oprogramowaniem?
M.: – Daleki byłbym od tego, żeby mówić o robotach i wdrożeniu. Samo funkcjonowanie idei Przemysłu 4.0 zakłada modernizację w pewnych obszarach, natomiast niekoniecznie w danym przedsiębiorstwie potrzebujemy robota. Może się pojawić potrzeba na inną funkcjonalność, np. scalenie bazy danych, system identyfikacji pracownika, może to być system przepływu informacji pomiędzy produkcją a managementem firmy. Hasło „robot” zawsze się kojarzy polskim przedsiębiorcom z kosztem. Oczywiście, jeżeli firma w wyniku audytu wykaże, że dane przedsiębiorstwo potrzebuje takiego robota zakupić, plus jego oprogramowanie, należy to wziąć pod uwagę. Gdy audyt wskaże, że można osiągnąć pewne efekty, które według właściciela firmy są konieczne do uzyskania przewagi technologicznej, a co za tym idzie – rynkowej, to skupiamy się na innych aspektach. To nie tylko kwestia robota i oprogramowania, ale również podejścia pod kątem zbadania potrzeb zakładu.
R.: – Czym jest system MES?
M.: – Jest to system do realizacji produkcji. Systemów zarządzania jest na rynku mnóstwo, natomiast system MES pozyskuje dane oraz pomaga w ich interpretacji bazując na danych z produkcji. Przykładowo: mamy fabrykę, mamy kilkanaście maszyn, kilkunastu pracowników i zadajemy sobie pytanie: jak wydajnie te maszyny pracują? To kluczowe pytanie, które można zadać każdemu właścicielowi firmy. Czy pracują na 70% swojej wydajności czy osiągają 100%, w jakich interwałach czasowych pracują i jak ta produkcja na maszynach się odbywa ilościowo i jakościowo. Jeżeli zadamy te pytania fabryce, która jest postawiona offline, gdzie maszyny nie są podłączone do żadnej sieci, zazwyczaj odpowiedź będzie następująca: potrzebujemy zebrać te informacje, ktoś to musi posprawdzać, pojawi się cykl tygodniowy badań i potem zostanie to zebrane i udostępnione. Systemy MES zbierają te informacje online. W trybie ciągłym monitorowania maszyny te informacje są przesyłane zbiorczo w jednym zasobie i następnie po analizie udostępniane w prostej i czytelnej formie końcowemu odbiorcy. Reasumując: to, co się dzieje w fabryce, na poszczególnych maszynach, ląduje w przeglądarce internetowej albo w dedykowanej aplikacji u człowieka, który zarządza daną linią czy fabryką w formie prostej do wyciągania wniosków.
R.: – Jak w kontekście Przemysłu 4.0 wygląda zapotrzebowanie na nowe kompetencje u pracowników? Czy potrzeba nowych kompetencji, nowych szkoleń, nowych kadr?
M.: – To zależy od specyfiki firmy i tego, jakie zasoby ludzkie posiada. Jeżeli mamy w firmie ludzi, którzy posiadają technologiczną wiedzę, to wystarczy przeprowadzić odpowiednie szkolenia. Jeżeli jest to firma, która nie posiada takich zasobów, wówczas mamy dwa rozwiązania. Albo zatrudnienie osoby, która jest wykwalifikowana na takim stanowisku, albo od podstaw przeszkolenie w takim zakresie. Jest to kwestia o tyle istotna, że jesteśmy świadkami ewolucji rynku. W tej chwili, patrząc na przykład paneli operatorskich, wyposażając stanowiska w HMI, przeszkalamy pracowników produkcji z obsługi. Analogiczna sytuacja występuje z pracownikami wyższego i niższego szczebla. Prowadzimy szkolenia tego typu pracowników w zakresie obsługi systemów czy aplikacji dedykowanych pod Przemysł 4.0. Nawiązując do pytania, jestem przekonany, że pracownik odnajdzie się w nowej technologii. Sama pandemia wymusiła na nas wszystkich pewien krok cyfryzacyjny, pracownicy, którzy dotychczas nie używali nowych technologii, zostali poniekąd zmuszeni do wdrażania się w nowe technologie. Praktyka pokazała, że z chwilą, gdy pojawia się taka potrzeba, nowe technologie dość szybko przyswajamy. Niemniej nowa klasa inżyniera niewątpliwie rośnie, istnieje na rynku potrzeba inżyniera nowej generacji, ale jest to nierozerwalnie związane z pędem technologicznym. Na ten moment, jeżeli zrobimy retrospekcję 10, 15 lat wstecz, kompetencje na rynku inżynierów były następujące: znajomość oprogramowania cad, znajomość języka angielskiego i szereg umiejętności związanych z produkcją. Obecnie coraz częściej pojawia się znajomość podstawowego języka programowania. Wynika to z faktu, że nasze społeczeństwo w dobie cyfryzacji poszukuje ludzi o takich kompetencjach. W wymaganiach na stałe zagości znajomość języka programowania oraz obsługi bazy danych. Za 5, 10, 15 lat te umiejętności będą standardem wymagań. Przez to klasa inżynierów związanych z Przemysłem 4.0 czy nowymi technologiami wyklaruje się samoistnie. Taka będzie potrzeba rynku.
R.: – Czy przedsiębiorca decydujący się na taką współpracę może liczyć na późniejszą obsługę techniczną?
M.: – Model biznesowy wdrażania takiego oprogramowania zależy przede wszystkim od przedsiębiorcy i od tego, jakie zasoby i jakie potrzeby są u niego wykazane. Jeżeli przedsiębiorca chce prosty model jakiegoś oprogramowania do prostej analizy, jak najbardziej taki model wdrażamy jednorazowo. Rzeczą oczywistą jest to, że musimy przeszkolić użytkowników końcowych, żeby umieli obsługiwać to oprogramowanie. Po spełnieniu tego warunku produkcja może ruszyć. Patrząc na dynamikę rynku, gdzie codziennie mamy styczność z tym, że urządzenie się aktualizuje, pojawiają się nowe funkcjonalności, rozszerzenia, tym samym zapotrzebowanie na ten typ usługi będzie rosło. Jeżeli świadomość dyrektora fabryki w związku z przeprowadzanymi wdrożeniami z biegiem czasu będzie rosła, to zapotrzebowanie na dodatkowe usługi z pewnością się pojawi, na co mamy nadzieję, ponieważ każda dodatkowa usługa, jeżeli tylko jest kompatybilna z profilem działalności producenta i przynosi mu wymierne efekty, jest i dla nas, i dla przedsiębiorcy funkcjonalnością strategiczną. Zakładamy, że podstawowy model działa w oparciu o pewien „core”, o niezmienne źródło, natomiast dalsze wdrożenia zależą tylko od tego, jak dana fabryka będzie się modernizowała, co na pewno nastąpi.
R.: – W jaki sposób firma Multiprojekt może pomóc przedsiębiorcom w cyfryzacji i robotyzacji przedsiębiorstw produkcyjnych?
M.: – Nasza firma posiada wieloletnie doświadczenie w dziedzinie automatyzacji przedsiębiorstw. Obecnie natomiast główny nacisk kładziemy właśnie na cyfryzację produkcji. Możemy zaproponować kompleksowe rozwiązania z zakresu Przemysłu 4.0, a naszym najmłodszym dzieckiem, a zarazem konsolidującym pod względem przepływu informacji ogniwem w pełni zrobotyzowanej linii produkcyjnej, jest autorskie oprogramowanie do realizacji produkcji Omnimes. Zapraszam do odwiedzania naszej strony internetowej www.multiprojekt.pl, gdzie wkrótce ukaże się więcej materiałów na ten temat.
Rozmawiał Jakub Łozowski – robotyka.pl
Multiprojekt Automatyka Sp. z o.o.
ul. Pilotów 2 E
31-462 Kraków
tel. 12 413 90 58
fax 12 376 48 94
e-mail: info@multiprojekt.pl
www.multiprojekt.pl
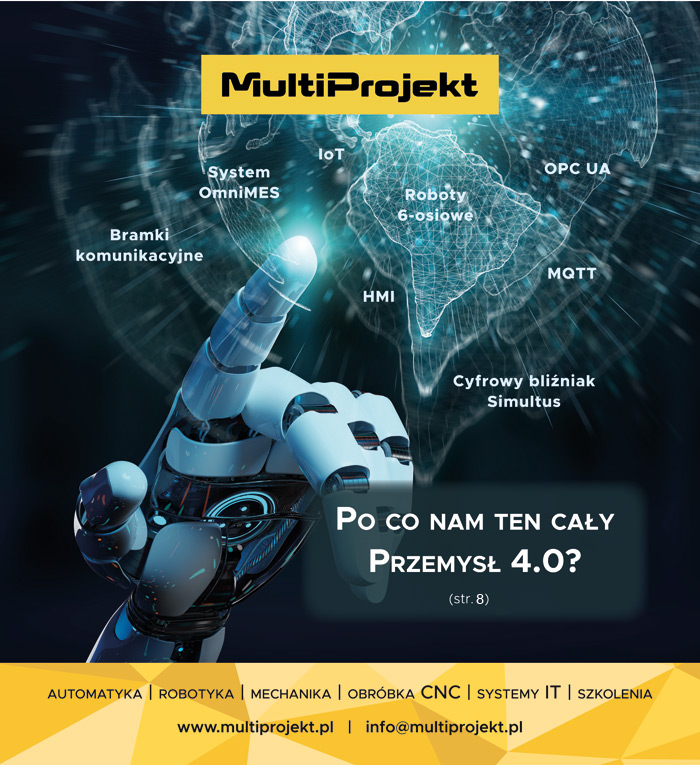